文:小川 勤/まとめ:ヘリテイジ&レジェンズ編集部/取材協力:ケイファクトリー
※本企画はHeritage&Legends 2022年11月号に掲載されたものです。
手曲げのような曲線を機械曲げで実現する!
エンジンから緩やかな曲線を描きながら集合部に繋がるケイファクトリーのチタン製エキゾーストパイプ。直線やカクッと不自然に曲がった箇所はどこにもなく、見ていると排気の流れのスムーズさまでが伝わってくるような気がしてくる。
「アフターマーケットで販売されるマフラーのカッコよさは第1にエキパイの美しさにあると思うんです。僕は若かった頃、高価な手曲げのマフラーが買えなかった。そんなトラウマかもしれませんが」と言うのは、ケイファクトリー代表の桑原さん。確かに最近は少なくなったが、手曲げなら排気効率の良い美しい曲線を描くことは可能だ。しかし、手曲げは文字通り職人による手作業のためコストもかかるし、技術の差が性能に影響してしまうこともある。
対して、近年主流となった機械曲げは、ベンダーという機械でパイプを曲げる製法。ただし、一般的なベンダーは曲げと曲げの間に必ず直線部分を取る必要があり、どうしてもカクッと曲がったラインが存在してしまう。これは純正マフラーを含め、さまざまなエキパイを見れば分かると思う。しかし、機械曲げは大量生産が可能で、仕上がりも性能も均一にできるメリットもある。
そこでケイファクトリーは手曲げの曲線美と機械曲げのメリットを活かそうと、1999年頃から独自の開発プロジェクトをスタート。当然、従来のベンダーでは思い描く曲げは実現できないため、3Dベンダーを導入。しかし、それでもなかなかうまくいかなかったという。
下に示した連続写真で分かるように、3Dベンダーはパイプを押し出す速度と方向を変えながら連続的にパイプを曲げる機械。だから直線部分がなく美しい曲線を描けるのだが、開発当初はベンダーメーカーでも鉄パイプを曲げる実績しかなく、薄くて硬いチタンパイプを曲げることは至難の業だった。
「パイプのシワや割れ、真円度を出すのに2年という期間がかかりました。テスト&トライに何千万円ものチタンパイプを廃棄しましたが、当時のウチは手曲げチタンマフラーを日本一生産していました。同じチタン材でも曲がりのクセが違うことを知っているなど、ノウハウが生きましたね」と桑原さん。
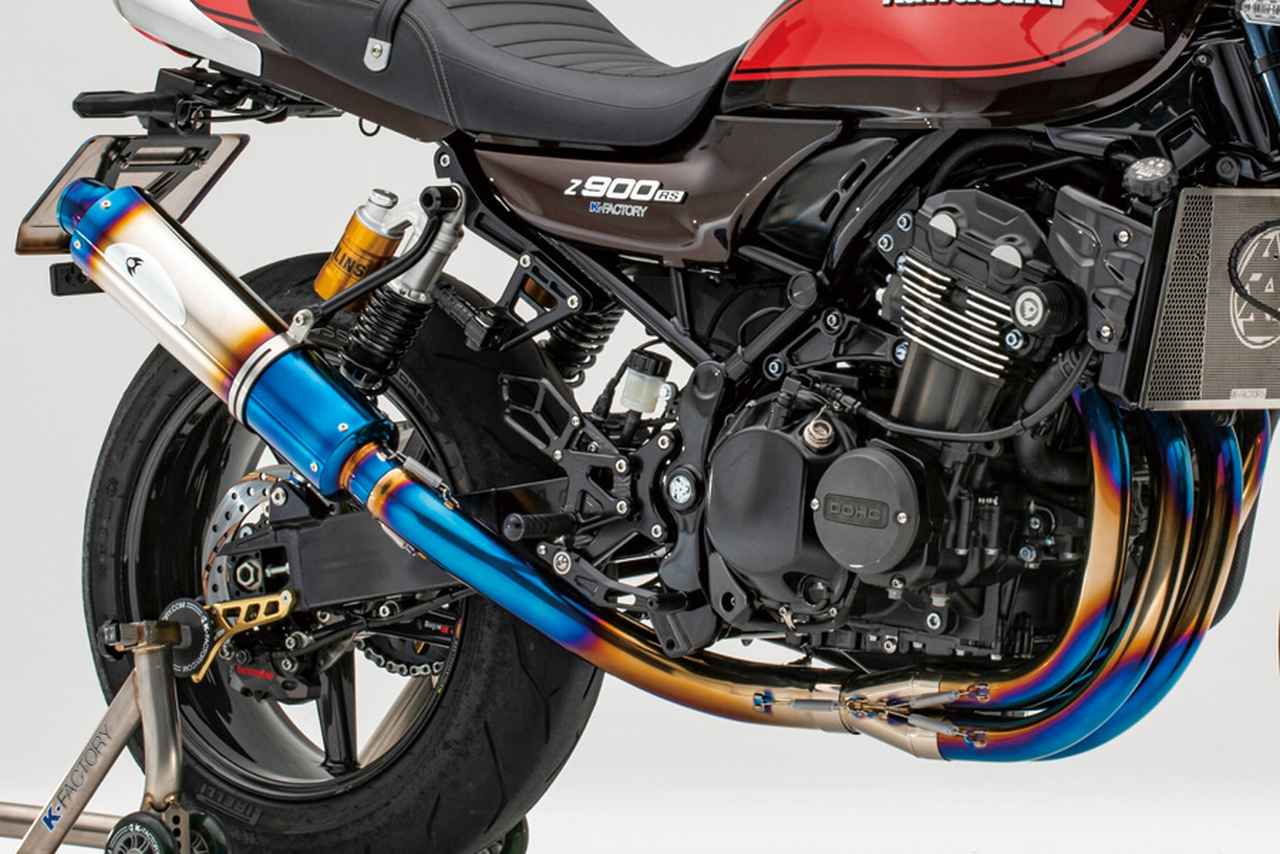
▲シリンダーヘッドから集合部にかけて優美な曲線を描く、ケイファクトリーの3Dベンダーで製作されたチタン製エキゾーストパイプ。写真はZ900RS用。φ42.7㎜と太めのパイプを使うのはカッコいいからだ。「マフラーはエキパイを作るのが一番難しい。だからこそ、そこにこだわりたいんです」と桑原さんは言う。
その3Dベンダーをモノにして、業界で最初にバフをかけたチタンパイプに青い焼き色を施したマフラーを発売。さらにそのエキパイにとどまらず、テールパイプやサイレンサーにも焼き色を付けたケイファクトリーのフルエキゾーストは大ヒットした。今はゴールドの焼き色も実現。他にない高級感で、その存在をアピールし続ける。
▶▶▶ヘリテイジ&レジェンズが取材した最新のカスタム・バイクはこちら!
自ら開発に携わった3Dベンダーは、手曲げよりも美しい機械曲げを実現
3Dベンダーを使ってチタン製パイプを曲げこんでいく作業。薄くて軽いチタンパイプを曲げられるようになるまで、2年もの月日を要したという。パイプ自体の材質選びはもちろんのこと、そのパイプを曲げるタイミングや入力の具合、方向を決めるのに手曲げで培ったノウハウが役立ったのだ。
▶▶▶ヘリテイジ&レジェンズが取材した最新のカスタム・バイクはこちら!
治具に装着して仮付け。その後、パイプを研磨へ
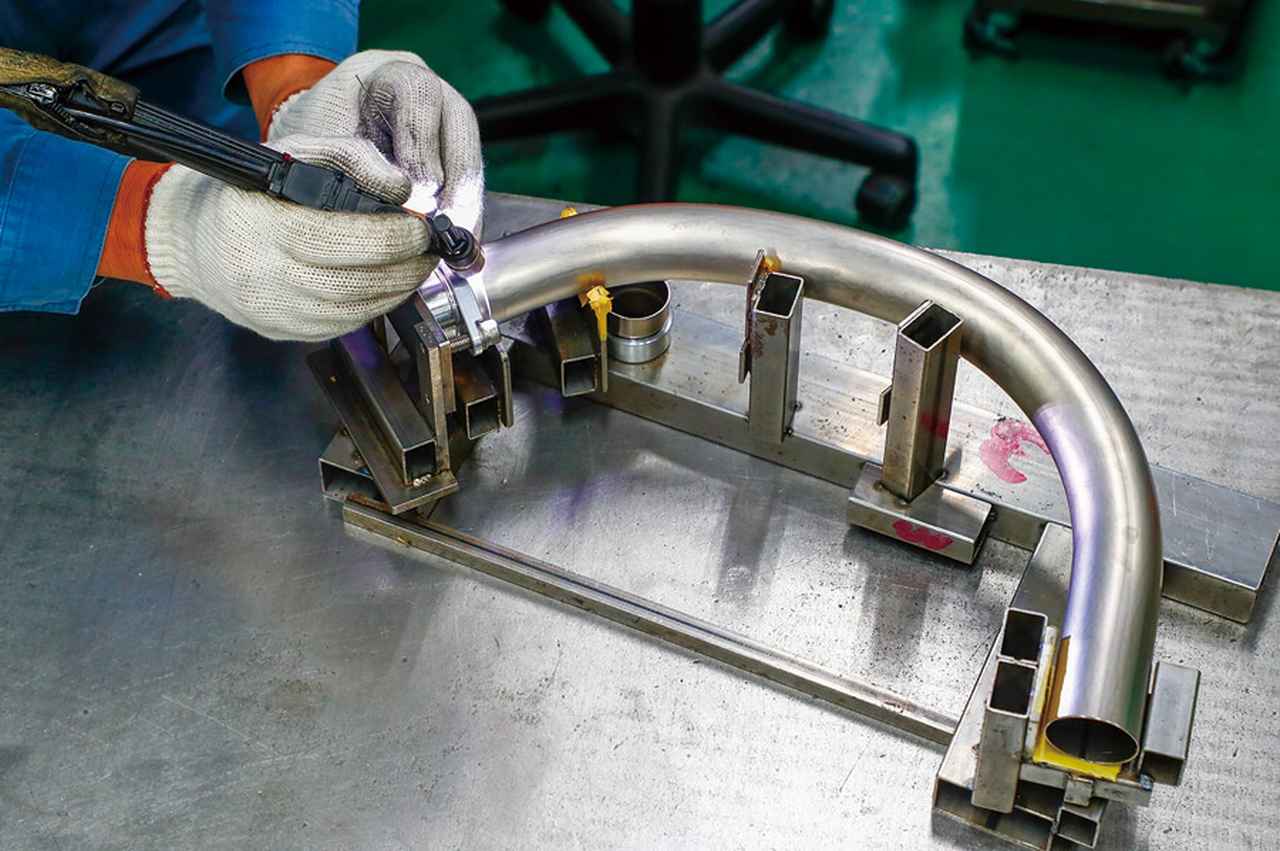
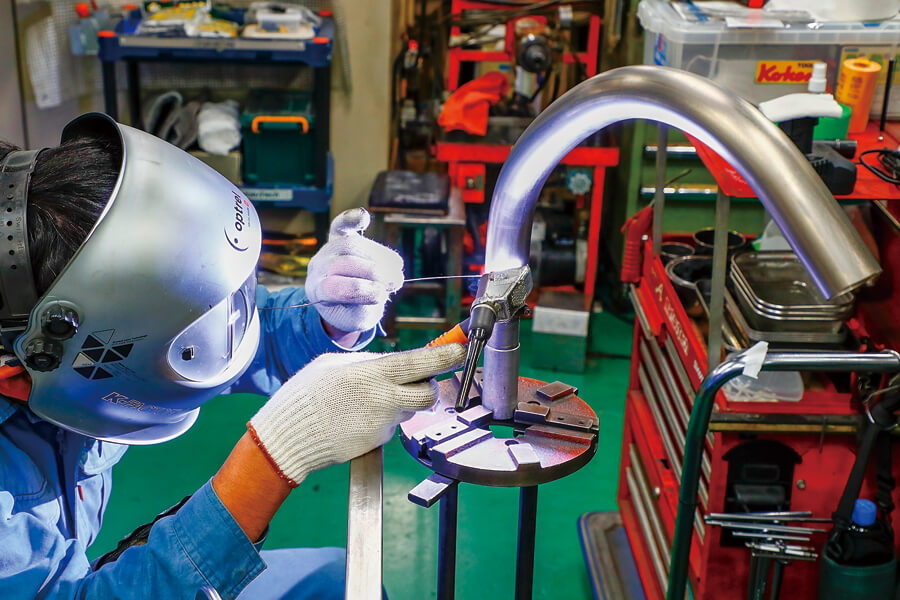
3Dベンダーで曲げ終えたパイプをカットしたら、治具に載せて仮溶接。その後、オリジナルの電動ろくろで全面を溶接する。マフラー製作の際は最初にノーマルの寸法を計測して、それを基にオリジナルのレイアウトを形成していくのだという。
▶▶▶ヘリテイジ&レジェンズが取材した最新のカスタム・バイクはこちら!
集合部分やビレットパーツなどマフラーの部品は自社生産
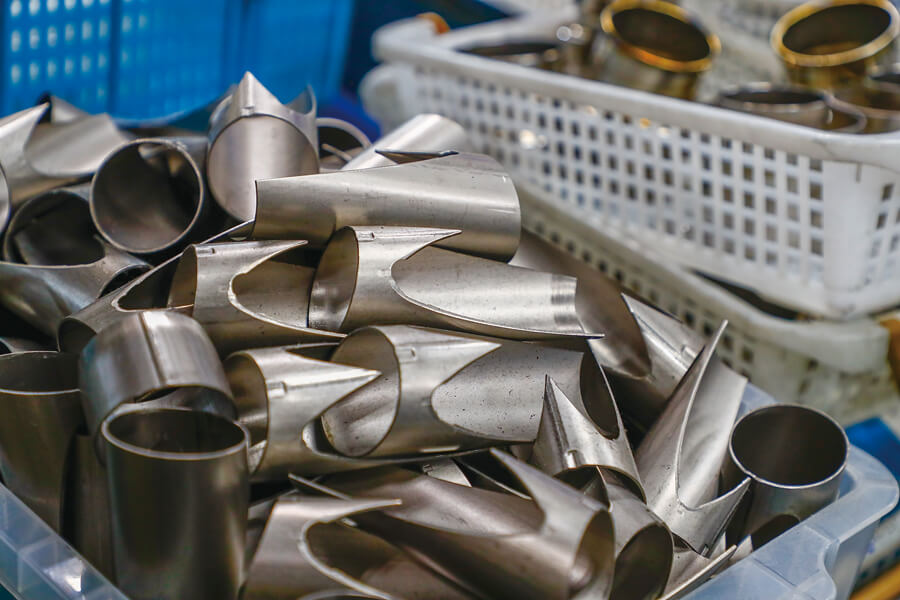
マフラーに使用する部品はすべて自社生産。集合部は様々な機械を組み合わせて自動で溶接する。集合方式はほとんどが4-1。それは、4-1集合は音が良く走っていて気持ちが良いから。『スタイルと音』、ケイファクトリーはその趣味性にこだわり続ける。
▶▶▶ヘリテイジ&レジェンズが取材した最新のカスタム・バイクはこちら!
煌びやかなブルー&ゴールドは熱を加えることで出現する
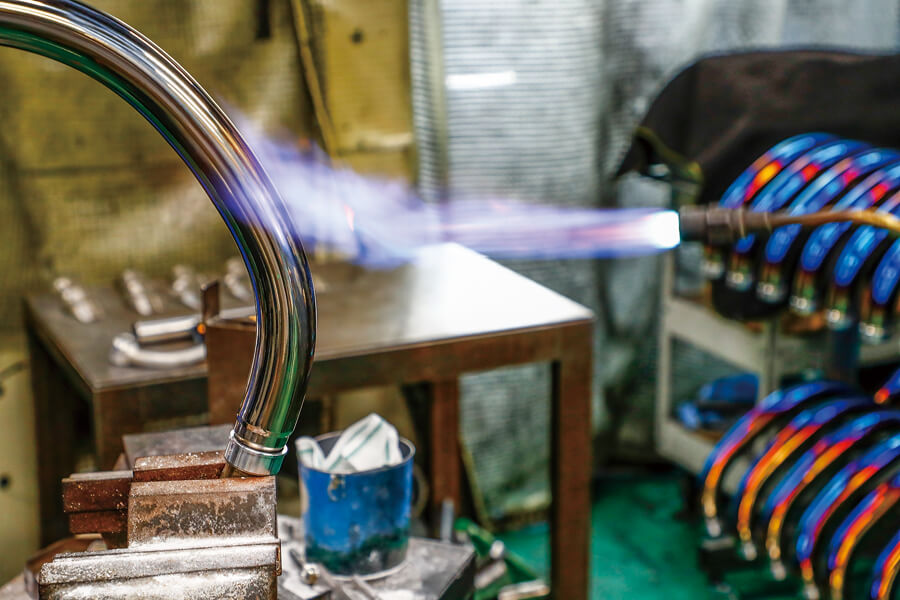
素材表面の余分な油や汚れを脱脂した後、バーナーで炙りながら焼き色を付けていく。ブルーをさらに焼きこんでいくとそのカラーはゴールドに変化。チタンパイプは温度や熱の伝わり方によって色が変わるのだが、それを製品に反映していくにはもちろん、熟練した技術を要するのだ。
▶▶▶ヘリテイジ&レジェンズが取材した最新のカスタム・バイクはこちら!
青い焼き色付きマフラーの草分け! 現在はゴールドもラインナップする
左はゴールド焼き付けで人気のCLR-RG+ フルエキ ヘキサゴンサイレンサー(29万1500円)、右は同社定番青色焼き付けのCLR-R+ フルエキ オーバルサイレンサー(25万8500円)。ともに車検対応のJMCA認証品だ。
文:小川 勤/まとめ:ヘリテイジ&レジェンズ編集部/取材協力:ケイファクトリー